今年5月初,科达承建的新润成600×600×9mm、双零吸水率渗花砖生产线,在稳定运行一个多月后,创造了天然气能耗最低1.13m³/㎡的记录,同时电耗也比旧窑减少20%; 2020年,中鹏热能为福建豪山企业改建的300×600×7.5mm中板生产线,实现天然气能耗低于1m³/㎡; 早在2019年,由德力泰承建的清远蒙娜丽莎800×800mm双零吸水率全抛釉生产线,全线天然气综合能耗维持在1.55-1.6Nm³/㎡; …… 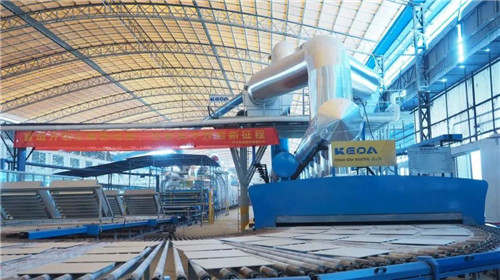
▲ 科达承建的新润成三公司(汇强陶瓷)渗花砖宽体窑。 近年来,瓷砖产能过剩问题日益突出,产品工艺技术高度成熟下的产品同质化引发激烈的价格竞争,但瓷砖生产综合成本却在持续攀升,这极大挤压了陶瓷企业的利润空间。于是,在保障产品品质的前提下,通过节能降耗降低生产成本成为了越来越多陶瓷企业追求的目标。 与此同时,在“碳达峰、碳中和”政策要求下,能源消耗总量和强度受到严控,这也要求陶瓷企业不得不减少能耗,甚至今年不少新建、改建项目因能评未通过被暂缓。 燃料成本普涨超10% 能耗引起陶企关注 佛山市德力泰科技有限公司副总经理荆海山算了一笔账:在全国陶瓷厂普遍烧煤的时候,煤价大致600多元/吨,按照1吨粉大约产33㎡瓷砖,用于生产最常规的800×800mm瓷砖计算,喷雾塔需耗煤55公斤,即大约1.7公斤煤/㎡,宽体窑大约能耗约为3.3公斤煤/㎡,合计燃煤成本还不到3元/㎡,这在瓷砖生产成本中占比比较小,是否节能所造成的成本差异不大,而且不易量化,因此很少引起企业足够重视。 多位行业人士认为,引起陶瓷企业重视能耗的转折点是天然气的普及,从2014年福建晋江成为第一个全面推行“煤改气”的产区后,2016年以来,山东、四川、辽宁法库、河北高邑、广东等陆续实施天然气改造,如今全国使用天然气的陶瓷企业数量已经过半。天然气相对煤炭,热值稳定,易于管理和统计,可以更好地量化能耗在生产中所占的成本比例。 “同样800×800mm瓷砖,窄体窑改用天然气后,需要大约2Nm³天然气/㎡,如果天然气价格按2.5元/m³计算,即使喷雾塔还是烧煤,总体成本也将上涨10%左右。”荆海山进一步计算到。 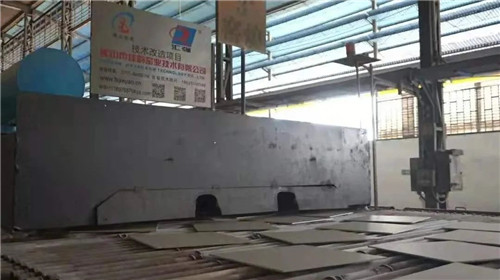
▲ 煤改气带来的成本上涨,大量陶瓷企业不得不通过技术改造实现节能降耗。 不仅燃气企业,燃煤企业如今也未能独善其身。“去年10月份的时候煤价大概800元/吨,今年高达1200元,光是这部分上涨的成本就能可以造成陶瓷企业综合成本上升12~13%,没几个企业能承受得住,因此必须从自身出发把成本降低。”佛山市科达机电有限公司总经理助理何卫东认为,成本压力促使陶瓷企业开始重视用节能减耗减低生产成本。 此外,国家发改委在《关于加强高耗能、高排放建设项目生态环境源头防控的指导意见》,明确“两高”项目暂按煤电、石化、化工、钢铁、有色金属冶炼、建材等六个行业类别统计,作为大建材行业的重要组成部分,陶瓷行业也正式进入“两高”之列,成为能源消费总量和强度双控的重点行业之一。 事实上,多地在“碳达峰、碳中和”的政策背景下,今年以来,纷纷出台了对陶瓷行业能耗的管理规定,大量新建、改建项目因能评而暂缓,这对陶瓷行业而言,又将掀起一次新的节能减排革命。 设备更迭,技术创新 造就节能降耗新高峰 天然气改造初期,大多数企业仅仅通过管道改造、更换喷枪等方式完成能源更迭,但过高的能耗使得企业难以承受,倒逼行业进行深入的节能研究,其中设备的创新和更迭起到了很大的作用。 “以前一些大产区很多窑炉已经用了十多年,从产能、产品配套、保温效果来说,已经不适合市场发展了,促使企业对生产设备、生产工艺进行迭代。”何卫东介绍,2019年以来,从广东、山东开始再到江西、四川等产区,设备更迭现象非常普遍,新设备和新技术已经将节能作为重点研发方向。 “同样烧天然气,生产同等规格的600×600mm、800×800mm抛釉砖,按照每公斤瓷能耗计算,我们国内普遍需要500大卡/公斤,而印度普遍则只需要400大卡/公斤,我们还高25%。”荆海山分析,国内瓷砖窑炉单位能耗高与窑炉设计较偏长,产量偏大有主要关系,在国内高温快烧的烧成制度下,预热区温度设置过高,导致排烟温度高,外排热量浪费多,再加上长窑正压大散热面积增加,大大造成了热量浪费而不节能。 荆海山指出,要降低能耗,首先烟气排放量要减少、烟气温度要降低,另外就是燃料的有组织燃烧。因此,无论是包括科达、德力泰在内的窑炉公司,推出了高精度的节能烧嘴,并通过空燃比例燃烧系统、助燃风加热系统使得燃烧更合理、高效。 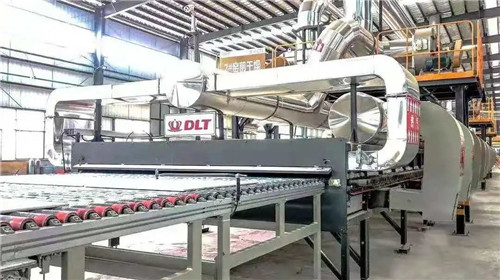
通过余热高效回收利用系统实现热量回收更是如今窑炉的标配。瓷砖生产过程中,制品温度从常温升到1230℃,然后再冷却降到100℃左右出窑,这其中冷却散发的热量有着极大的回收利用空间。 另外,荆海山认为,窑炉热平衡里,排烟带走热量占总能耗约20~30%,如果直接排到脱硫塔,不仅浪费还增加了末端治理的成本,现在通过烟气换热器的热交换后,可回收烟气热量的50-60%热量,再输送到干燥器做加热利用,基本实现窑炉烟气与余热热量的高比例回收,基本实现干燥零能耗。 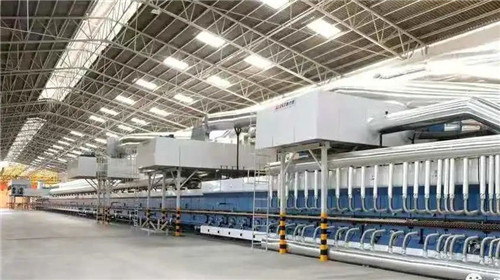
▲ 德力泰全余热回收系统。 纳米粉、纳米绝热板/砖等窑炉新型隔热材料的升级也极大减少了热量的散失。何卫东介绍,2015年左右很多窑炉、窑顶温度都到了100多℃,现在通过设计和用材,可以控制到70多℃;窑墙外侧的温度已经不超过60℃,这充分说明保温效果作用更好了,对节能有很大的作用。 除了节能,在节电方面,荆海山同时介绍到,风管路的合理设计降低了气体流速,减少了阻力,使得风机低频运行大大节省了电耗。 同时在窑后环节,实现窑后整线PC控制,在电耗上也实现了接近20%的减耗作用。据了解,在窑后各环节中设备如果持续运行,抛光环节综合运行效率大约为80%,包装线大约是60%,储砖线则不足50%。而科达正通过窑后整合创新改变这一现状。通过总控的方式提高设备综合运转效率,用PC把后段设备管控起来,不仅提高了设备的稳定性、智能化,还大大节省了用人数量和电耗。 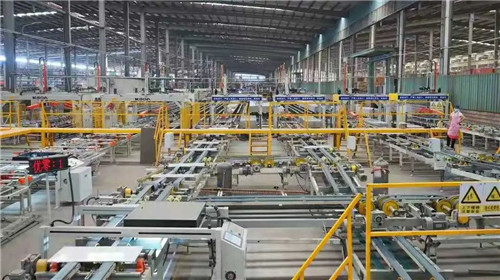
▲ 窑后整线。 产品减薄、配方优化 低温快烧实现低耗能 除了通过精准管理以及上游设备企业研发的新技术应用外,陶瓷企业自身通过产品创新也在节能降耗上取得显著效果。 “印度比我们能耗低,其中一个原因就是他们的产品比较薄,我们普遍10.2mm的常规800×800mm抛釉砖,他们的厚度大概是9.8mm,加上产品配方工艺也不一样,能够低温快烧。”荆海山认为,瓷砖薄型化一定是未来的发展方向,这不仅起到节能的作用,还能节省资源。 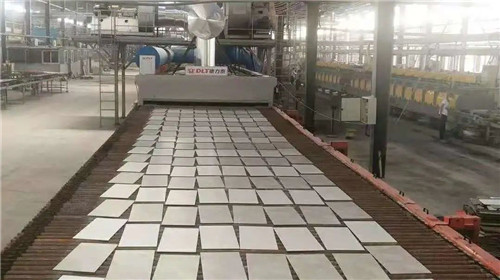
▲ 中板是瓷砖减薄的创新产品,图为德力泰承建的四川利弘中板生产线。 如今,中板、薄板的发展也印证了这一说法。何卫东介绍,科达在福建新建的一条薄板线,天然气能耗最低达到了1.12m³/㎡。根据《陶瓷信息》了解,目前逐渐成为陶瓷行业主流产品的7~8mm中板,能耗可降至1.2m³/㎡以下。 专业从事窑炉技术改造的佛山市佳韵窑业技术有限公司总经理程昭华在经历了大量陶瓷企业技改项目后发现,陶瓷企业也在通过降低产品成本,比如减少更多超白高温原料的使用,实现低温快烧以达到降低能耗的目的。 能耗屡创新低 三年可省出一条新窑炉 综合性的节能降耗效果跟传统生产线能耗相比有多大差别?能给陶瓷企业带来多大的效应? 以天然气改造为例,普遍认为,生产800×800×(10.5~11)mm单零吸水率抛釉砖,根据窑炉长度和宽度不同,旧窑改用天然气后能耗基本在1.8~2m³/㎡。 程昭华介绍,最早改用天然气的陶瓷企业,由于没有生产经验,生产常规800×800mm瓷砖,经常会出现能耗高达2.6~2.8m³/㎡的情况,但通过节能改造,如今最低可降低至1.6m³/㎡。 “我们去年低在江西新建的一条混烧800×800mm、600×1200mm抛釉砖生产线,日产量4.7万㎡,使用天然气。按照以往的经验,这么大产量的生产线,使用水煤气普遍需要3.5~3.8m³/㎡,换算成天然气大概是1.9m³/㎡,但实际我们做到了1.65-1.7m³/㎡。”何卫东指出,通过设备升级,节能效果在大产能生产线中也取得了显著的效果。 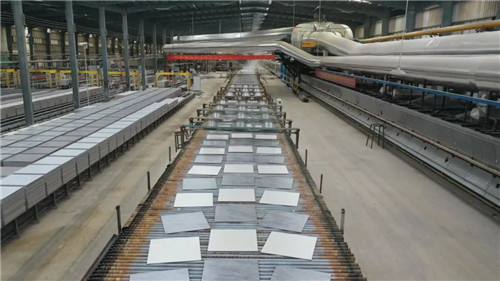
▲ 科达承建的日产4.7万㎡抛釉砖生产线,能耗可达1.65-1.7m³/㎡。 尽管对大多数产区和企业而言,充分的节能降耗并不能完全抵消改用天然气后上涨的成本,但相比旧窑直接使用天然气,对比效果却十分明显。以德力泰承建的清远一家陶瓷企业全新的一条双零吸水率的800×800mm抛釉砖生产线为例,改用天然气后,企业旧线窑炉天然气能耗基本为1.9m³/㎡左右,新建窑炉能耗目标为1.6m³/㎡,实际做到了1.55m³/㎡。 “按照当时的天然气价格2.5元/㎡,能耗成本就有将近1元/㎡的差距,一天产量大约1.2万平方米,一年就大约可节省360万元,通过能耗的节省,3年多时间就可以把生产线的投入收回。”荆海山认为,当时双零吸水率的常规800×800mm抛釉砖能耗从2m³/㎡降低做到1.6m³/㎡以下,是具有划时代意义的。 在众多业内人士看来,在“碳达峰、碳中和”的大背景下,节能降耗将是被列为“两高”项目的陶瓷行业很长一段时间的重要课题,也是目前较好的减排解决方案,无论是新建还是技术改造的生产线,得益于节能技术的进步和精细化管理,在产品品质提升的同时,实现低碳与节能增效的叠加效果,促进企业可持续发展,同时也创造了更大社会价值。 (本文转载自陶瓷信息) |