我国建筑卫生陶瓷行业贡献了全国GDP的1%,消耗了全国能源的1.7%,其中竟包括消耗全国30%的天然气资源,而天然气是稀缺资源,全国超过50%的天然气都需要进口。巨大的投产比落差,使得建筑卫生陶瓷行业的能源利用效率饱受诟病。 随着我国对全世界做出了“2030年、2060年分别实现碳达峰、碳中和”的承诺,如何进一步节能减排成为各行各业的重点工作。 对此,中国建筑卫生陶瓷协会指出,工业燃气比率在2025年后不予增加,2030年后比重减少,天然气是碳中和的过渡能源,电力将成为未来的“能源主力军”,电烧窑炉(以下简称“电窑”)将是建筑卫生陶瓷行业能源技术发展的新方向。 那么,用电窑来生产瓷砖,究竟靠不靠谱? 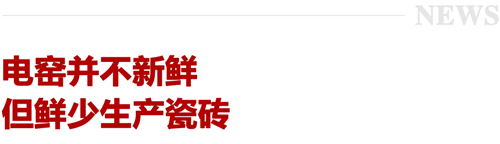
在瓷砖生产领域,窑炉是不可或缺的重要部件,陶瓷人见证过烧煤、重油、柴油、煤制气、天然气等碳基燃料的窑炉,但很少见到烧电的窑炉。 佛山科达机电技术中心总监潘建环介绍说,在上世纪九十年代他就已经接触过生产日用瓷的电窑;近年来,科达在国内外均有电窑的实际应用案例,比如在法国有生产微晶玻璃的电窑案例,国内有生产锂电池的电窑案例。 可见,电窑实际上并不新鲜,在从事窑炉研发创新的专业人才眼中,电窑是其工作的一部分。佛山佳窑总经理程昭华指出,电窑的应用范围很普遍,技术也已经很成熟,只是很少用于瓷砖生产,而是广泛应用在磁性陶瓷、特种陶瓷、锂电池、玻璃马赛克、三度烧K金砖、包裹色料等领域。 明眼人一看就已心领神会,上述领域都是高精尖、高附加值的产品,而且对产品的烧成气氛、物理化学性能等方面要求非常严格,因而用电窑能够更好地控制。 那么,电窑就没有瓷砖领域的实际应用案例吗?据了解,拉米娜(Laminam)俄罗斯分厂生产岩板的窑炉就采用了电和天然气混用的烧成方式。 潘建环也透露,科达在2015年就已经在俄罗斯有一条生产三度烧花片的电窑案例,先用1170℃烧素坯,再烧烤花。 
▲科达在俄罗斯的三度烧花片电窑案例。 既然技术很成熟,也有实际案例在前,为何在国内还没有一条瓷砖生产线采用电窑呢? 程昭华表示,电窑的特性是烧成速度慢、周期长,意味着其单位产量小(产值往往不小),目前还不太适合瓷砖这种规模化大生产的产品对窑炉的需求。 烧成速度慢、周期长的原因又是什么?程昭华进一步解释,烧天然气是以对流换热为主、辐射换热为副、传导换热为辅;而电窑则是以辐射换热为主、传导换热为副、对流换热为辅,而热交换效率最高的手段就是对流换热,如同在空调房里再加一个小风扇,这个小风扇会让人感觉非常凉爽,因此对流换热更适用于瓷砖等大规模生产的产品领域。 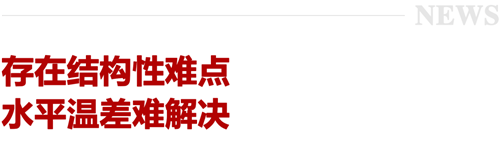
电窑若果真要大批量推广到瓷砖生产领域,首先需要跨越的技术沟堑,就是解决安装难题。 佛山德力泰副总经理荆海山指出,由于烧电主要是辐射传热,因此烧电比较适合安装在高温带,而高温带必须用硅碳棒来做,加热温度安全及耐用,但是硅碳棒目前只能做到3米左右长度,如今瓷砖宽体窑的内宽达到3米以上,硅碳棒就会面临结构性的安装难点。 此外,荆海山还表示,电窑内部截面的温差控制,以及高温辊上硅碳棒的寿命、更换、维护、安全等方面,都需要技术上的突破。 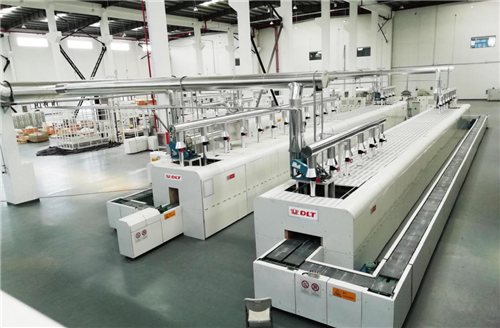
▲德力泰气氛式推板电窑。 程昭华也表示,水平温差将成为电窑生产瓷砖的技术难点,这是因为大批量生产的窑炉横跨面较宽,容易产生窑炉中间和两侧的烧成温度不一致的现象,遇到这种情况,烧天然气的窑炉加一个特制的燃烧器(俗称“喷枪”)就可以解决,但电窑是通过硅碳棒、硅钼棒或者发热丝来进行辐射传热,解决水平温差的难度就比较大。 不过,程昭华认为一旦要大批量使用电窑,集行业之力来攻克水平温差,肯定也会很快取得阶段性突破,比如在电窑下面增加一个类似修车的维修通道等特殊结构和发热装置,解决的方法一定会有很多。 对于电窑的上述结构性难点,潘建环表示,业内一直都有探讨解决方案,例如可以在瓷砖宽体窑炉正中间增加挂钩将硅碳棒挂住,以此解决硅碳棒长度不够的安装难点。另外,潘建环特别提到了能够破坏电网的谐波,一旦用电量很大,且瓷砖烧成需要经常调节电压来控温,这就需要安装类似变压器的滤波电容器,来杜绝电网过热而着火、短路的风险。 而与结构性难点相比,烧电的成本太高则是电窑推广的最大阻力。 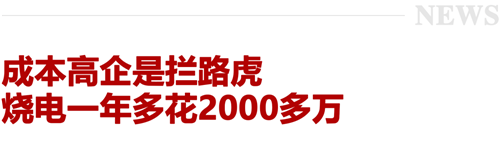
对于瓷砖产品本身来说,程昭华指出了电窑热能利用效率较低的痼疾,如果折算成现有窑炉所消耗的天然气产生的热能,电窑所消耗的电量将会非常巨大,如此一来,陶瓷厂的装机容量会非常高。 因此,从成本方面考虑,他认为在未来5年之内,大批量生产的瓷砖使用电窑的概率会比较小。 荆海山则透露了他的测算结果,一个日产20000㎡瓷砖的窑炉,仅仅是在高温带用电窑,装机容量要达到10000多千瓦,如此巨大的装机容量将会非常难以满足。 而关于用电和用天然气的成本比较,荆海山进行了一番细致的对比换算。不考虑发热设备的转化效率,烧1度电理论上可产生860Kcal热量,而烧1Nm³天然气低位发热值是8300Kcal热量,也就是说1Nm³天然气对应9.65度电发热量。 当前的平均每度电价是0.7元,9.65度电的电价是6.76元,天然气的价格往常只有2.6元/Nm³左右,现在最贵约4.3元/Nm³,如此一来,1Nm³的天然气价格要比9.65度电低2.46元,能源成本非常不对等,是推广电窑最大的难点。 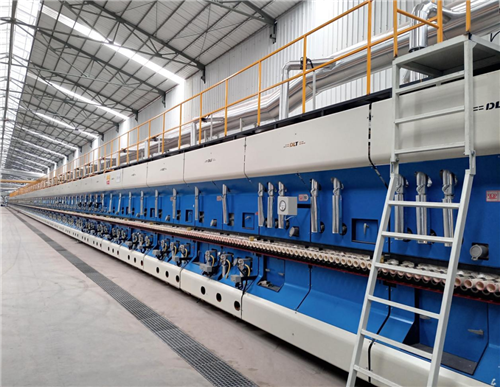
▲德力泰天然气岩板宽体辊道窑。 可别小看这2.46元的能源成本差价。荆海山指出,当前800×800×11mm的抛釉砖,每平方米瓷砖窑炉需要消耗的天然气在1.6Nm³左右,一条日产20000m³瓷砖的窑炉,一天需要消耗32000Nm³天然气(燃气费用137600元),换算成全部用电则是308800度电(电费216160元)。 可见,用天然气比用电每天就可节省78560元,每年按300天计就可省下2356.8万元。“差这么多的燃料钱,谁用得起?” 而且,即使不计成本,考虑到今年全国各大陶瓷厂区频繁出现的限电情况,广西产区甚至限电28天,瓷砖若是改用电窑,大幅度增加的用电量必将导致更大的电能供需矛盾。 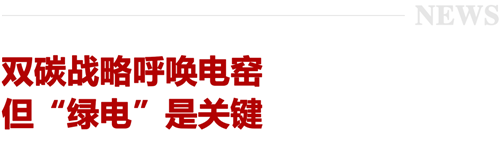
我国能源“富煤、贫油、少气”的状况众所周知。中国电力企业联合会7月8日发布的《中国电力行业年度发展报告2021》指出,2020年我国全口径发电量为76264亿千瓦时,其中火电为51770亿千瓦时占比全国67.88%,而火电中的煤电46296亿千瓦时占全国60.70%,此外水电占全国17.77%、并网风电占全国6.12%、核电占全国4.80%、并网太阳能发电占全国3.42%。 可见煤电仍然是我国电力供应的主能源。如果瓷砖全面改用电窑,未来数年必然也将依赖煤电,而只要烧煤就会产生碳排放,只是这些碳排放集中于上游的火力发电厂。 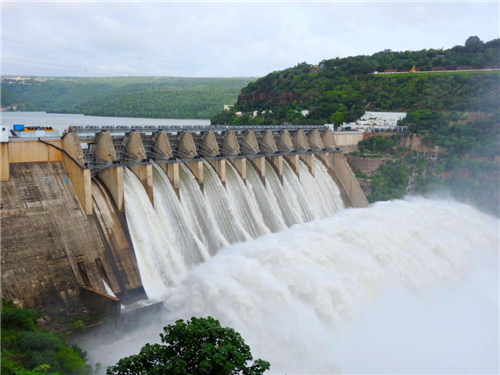
▲“绿电”才能让电窑实现真正减碳。 荆海山指出,1公斤标煤的发电量是3.3度,但是1公斤标煤燃烧会产生约2.7公斤的碳排放,从碳达峰、碳中和的减碳角度出发,电窑肯定是趋势,但最终还要考虑是否为“绿电”,如果未来风电、水电、光伏太阳能发电等“绿电”能够满足工业生产,彼时再考虑烧电才会符合实际发展情况,而当前的现状是工业用电不够,许多地方都在执行“开四停三”等限电措施。 程昭华表示,对于火力发电厂来说也有减少碳排放的压力,所以他们也要进行发电设备的更新换代与节能改造。《陶瓷信息》根据中国电力企业联合会官网发布的信息了解到,2020年全国单位火电发电量二氧化碳排放约832克/千瓦时,比2019年下降6克/千瓦时,比2005年下降了20.6%。 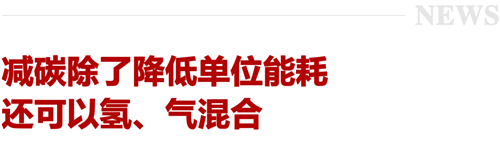
从宏观视角来看,碳达峰、碳中和是我国必须要向全世界交的答卷。但具体到瓷砖生产领域,考虑到限电等矛盾,节能减排的当务之急并非转换燃料,而是提高现有碳基燃料的单位热效率,还可以探索氢气和天然气混合燃烧的路径。 事实上,相比以往,生产每平方米瓷砖所需要消耗的天然气,近年来已有明显降低。据程昭华介绍,通过持续不断地改善窑炉结构和提高余热利用效率,如今,生产每平方米瓷砖已经从需要消耗3m³天然气,一路降到了1.6m³→1.5m³→1.2m³,程昭华所在的佳窑公司,仅通过技改,就帮助某陶瓷企业实现了1.16m³/㎡,这就是从成本出发实现的节能降耗。 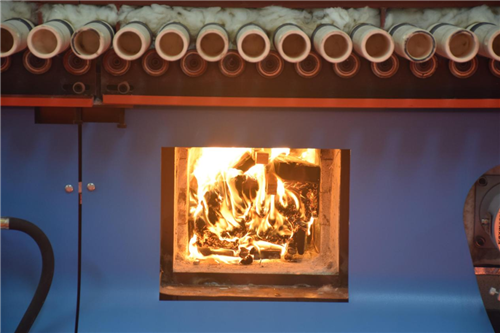
▲节能减排的当务之急并非转换燃料。 其他的窑炉公司也在节能方面持续探索。今年5月初,科达制造承建的新润成600×600×9mm双零吸水率渗花砖生产线,在稳定运行一个多月后,创造了天然气能耗最低1.13m³/㎡的记录,同时电耗也比旧窑减少20%。 在双碳战略的指导下,每个陶瓷厂正在面临严格的能评指标,如果想要增加产能,就只能提高能源利用率,降低单位能耗。 程昭华认为这是陶瓷行业的当务之急,也是未来5年内必须攻克的课题,如果能在每平方米瓷砖消耗1.2m³甚至1m³天然气的基础上,整个行业能够再进一步降低20%,那对双碳战略的贡献不言而喻。 对氢能源的探索也正在路上。2020年9月29日,广东省发改委等六部门印发《广东省培育新能源战略性新兴产业集群行动计划(2021—2025年)》,其中就指出要“推进佛山(云浮)产业转移园、广州开发区、佛山南海和高明区等氢燃料电池产业园建设,建立广深高温燃料电池及系统研发制造基地,建立广州、佛山、东莞、云浮氢能高端装备产业集聚区和惠州、茂名、东莞、湛江氢能制储运产业集聚区”。 据荆海山透露,德力泰正在探索氢气和天然气混烧窑炉,目前正在国内布局一个项目,该项目氢气占比50%多,可等量减少50%多的碳排放,这是因为1Nm³天然气接近1Nm³甲烷,1Nm³甲烷燃烧后产生2公斤二氧化碳,如果氢气占比50%和天然气混合,就相当于减少了1公斤的碳排放,而这减下来的碳在碳交易市场就是真金白银。 潘建环指出,今年业内对氢气的研究明显加快,科达也正在积极地探索氢能源如何利用。 此外,对于减碳而言,潘建环认为除了提高能源热效率,还有一种方法就是回收烟气中的二氧化碳,因为二氧化碳的用途很广,它可以做成干冰,啤酒汽水也需要,还可以用作植物肥料,石油采矿、机器铸造、金属治炼、生物制药、消防等各领域也都需要二氧化碳。 目前,建筑卫生陶瓷行业总体的碳排放量正在摸底调查,根据中国建筑卫生陶瓷协会公布的数据,每年约为1.4-2.0亿吨,其中建筑陶瓷占比96%。对此,荆海山认为建筑卫生陶瓷行业产能下降、产品升级、能源结构调整等三个趋势,都将助力建筑卫生陶瓷行业到2060年实现碳中和目标。 (文章转自陶瓷信息) |